Contents
First of all, the article will be useful to those who are just about to buy (choosing between several models) or have recently acquired a beer (BK) or distillation column (RK): they purchased a ready-made kit in a store, ordered it from masters on forums, or made one on their own from one of schemes. By comparing the characteristics of your column with the reference ones, you can check whether the equipment is ready for operation right away or if it needs to be upgraded.
Differences between distillation and beer columns
RK and BC are devices that implement the technology of heat and mass transfer. For the end user, the difference between them is only in the requirements for the quality of cleaning the drink from impurities. If for the RK the ultimate goal is alcohol according to GOST, then a well-purified distillate (moonshine) is obtained at the BK with the preservation of the aroma of the feedstock, but not pure alcohol. The methods for achieving the goal are the same.
A high degree of purification in the RK requires more time to complete individual operations, a better degree and clarity of separation into fractions. Therefore, the RC has a higher column and liquid extraction, which makes it relatively easy and inexpensive to automate the entire process. Not everyone is able to sit near the column for a day, and that is how long the process of rectification at home lasts.
Steam extraction is also possible for RC, but its automation is costly. In addition, the problem with stabilizing the water pressure in the dephlegmator calls into question the feasibility of using steam extraction for the RC, since liquid extraction is not so sensitive to water pressure drops.
In order to increase productivity for the Republic of Kazakhstan, it is advisable to use cubes with a capacity of 40-50 liters. For BC with their low columns and less holding capacity of fusel oil, the volume of cubes is limited to 20-30 liters. This reduces the distillation cycle on the BC to a time acceptable for manual control, which has allowed steam-bleed BC to gain popularity, although there are many fans of BC with liquid extraction and automatics.
RK and BC requirements for equipment
In pursuit of an attractive price, manufacturers issue a semi-finished product as a finished device that requires significant refinement before operation. For example, absolutely no thermal insulation. In this form, only an incorrigible optimist can expect a decent purification of impurities from the column.
Cube
The main function of the cube is the generation of alcohol-containing steam at the most stable speed, regardless of environmental influences. This ensures a constant speed of steam in the column.
At a constant steam speed, the number of separation stages in the packed column varies depending on the reflux ratio (FN). The number of separation steps is maximum at an infinite reflux number and equals zero at zero. Each PF value has its own number of separation steps.
Technological requirements for column cube equipment:
1. Warming. Must be careful, for example, using polyurethane foam with a thickness of 20-25 mm. From above it is useful to cover the thermal insulation with a layer of foil insulation. The substrate under the main layer of the heat insulator can be ordinary corrugated cardboard, which will significantly reduce the temperature and protect the foam or foam insulation from temperature sagging of the thickness.
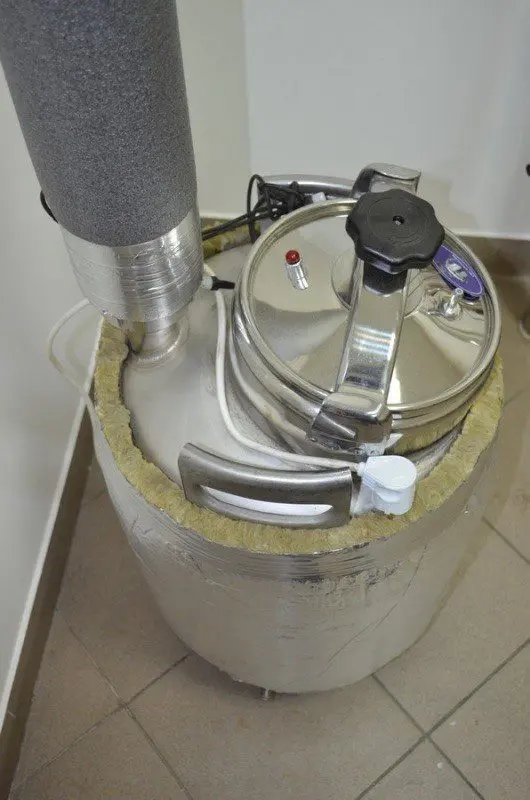
The figure shows an example of unsuccessful insulation of a cube with mineral wool, if it accidentally gets wet – the thermal insulation is over. In addition, heating and cooling the cube causes the thermal insulation to “breathe”, thereby sending dust into the room when heated, which is harmful to health, and when cooled, worsens the insulating properties.
It is important to pay due attention to the choice of material. Often the cube is wrapped over the insulation with ordinary cling film for waterproofing, protecting the surface from spilled water, mash or raw alcohol.
The need for thermal insulation is caused not so much by economic reasons as during distillation (less energy is spent), but by the fact that during the rectification process the amount of alcohol in the cube decreases, which increases the boiling point. As a result, at a constant heating power, by the end of the run, the heat loss of a well-insulated cube increases by 50-60 watts. This reduces the useful heating output by about 3%. With an uninsulated cube, this value can be up to 15-20%, which is a lot. Since the useful heating power cannot be measured during the process and corrected by the supplied power, this leads to an uncontrolled decrease in the amount and speed of steam in the column – exit from the most effective pre-choke mode and a decrease in the quality of separation into fractions.
2. Heating elements and voltage regulation. Heating should be carried out only by heating elements, using a voltage regulator with stabilization up to 1 Volt. Even in this case, at a voltage of 150 volts, the useful power can vary by up to 3%. Together with the thermal insulation of the cube, the stabilization of the heating power will limit the fluctuation of the steam velocity in the column within 5%. Which is more or less tolerable.
3. Proper location of the thermometer. The thermometer must be placed in a cube below the waterline, since to control the process you need to know the temperature of the liquid, not its vapor. By increasing the boiling point, the strength of the raw alcohol and the remainder of the absolute alcohol in the cube are judged, and this is also a signal for switching to the selection of “tails”. Successful placement of the temperature sensor in the thermoregulator tube of the heating element, bent from the heater by 3-4 cm to the side and slightly up. The temperature sensor is inserted into the tube on the thermal paste.
4. Legs adjustable in height. The column in the operating mode must be installed strictly vertically. Deviations lead to the fact that steam and phlegm find different paths – phlegm flows down the “lower” wall of the column, and steam rises along the “top”. It is clear that their interaction is minimal.
5. Additional elements. It is very good if the cube has a safety valve that relieves pressure in an emergency, and there is also a branch pipe for draining the stillage and convenient carrying handles. These improvements do not directly affect the result, but greatly simplify the work.
Column
The height of the distillation column should be 1,5 meters, the height of the beer column should be from 0,7 to 1 meter.
Any column must also be insulated. During operation, heat losses do not change, but good insulation reduces the amount of wild phlegm, significantly increasing the controllability and stability of the process as a whole.
To insulate the column, hemp or jute twine is suitable as the first layer, this will protect the main insulation from temperature deformations. As the main insulation, polyurethane foam, foamed polypropylene or polyethylene with a thermal conductivity coefficient of about 0,04 W / (m-K) is usually used.
The thickness should provide heat loss of no more than 3% of the operating capacity of the column. At 5%, wild phlegm almost completely disrupts the rectification process, since the separating capacity of the column falls catastrophically. At 10%, you can forget about rectification, only the appearance of the process remains.
To ensure normal thermal insulation for columns with a diameter of 32-60 mm, subject to an ambient temperature of at least +23 ° C, a layer of basic thermal insulation of at least 20 mm is required, if work is to be done at an air temperature of +10 ° C, thermal insulation must be doubled, at zero temperature – increase by 2,5-3 times. On top of the main insulation, it is desirable to put a layer of foil insulation 3-5 mm thick on the column. To isolate the seams, self-adhesive foil tape and fastening with clamps from below, from above, as well as in several places along the height of the column, are suitable.
Nozzle
The nozzle should provide the maximum area for heat and mass transfer. The most suitable for RK is SPN, its optimal dimensions depend on the diameter of the column. For BK, washcloths and tap changers are most widely used, their relatively low separating and holding capacity is compensated by low requirements for distillate in terms of purification degree and low cost.
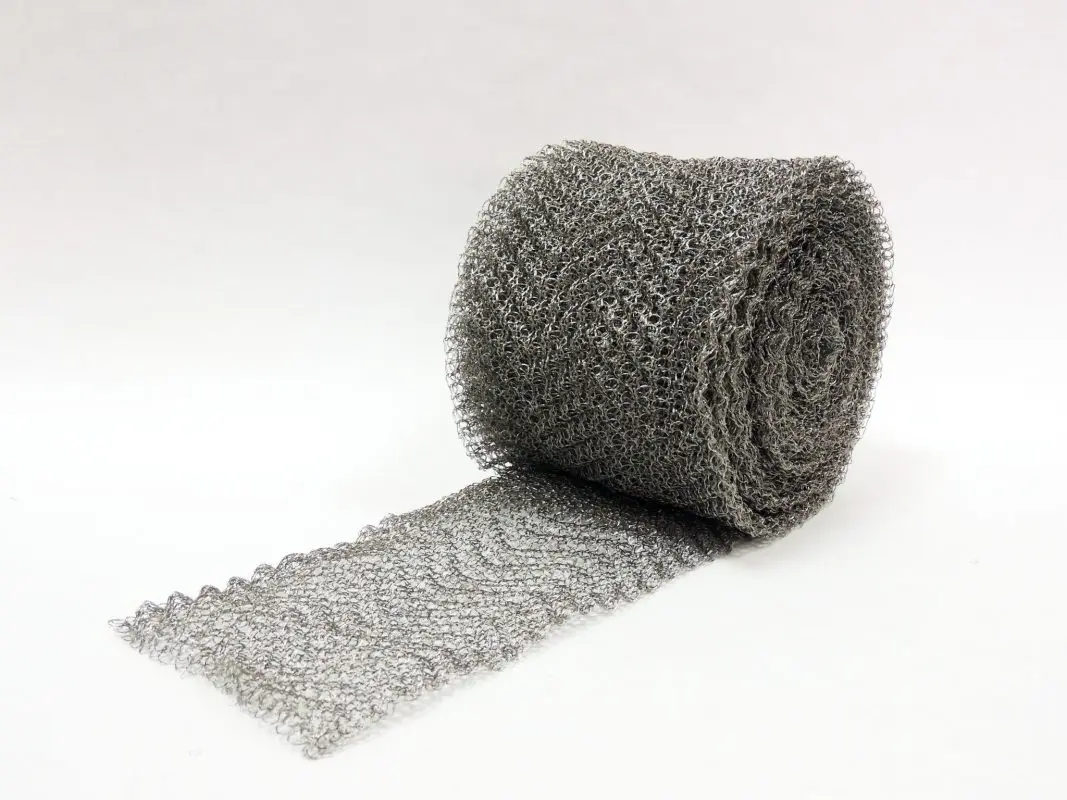
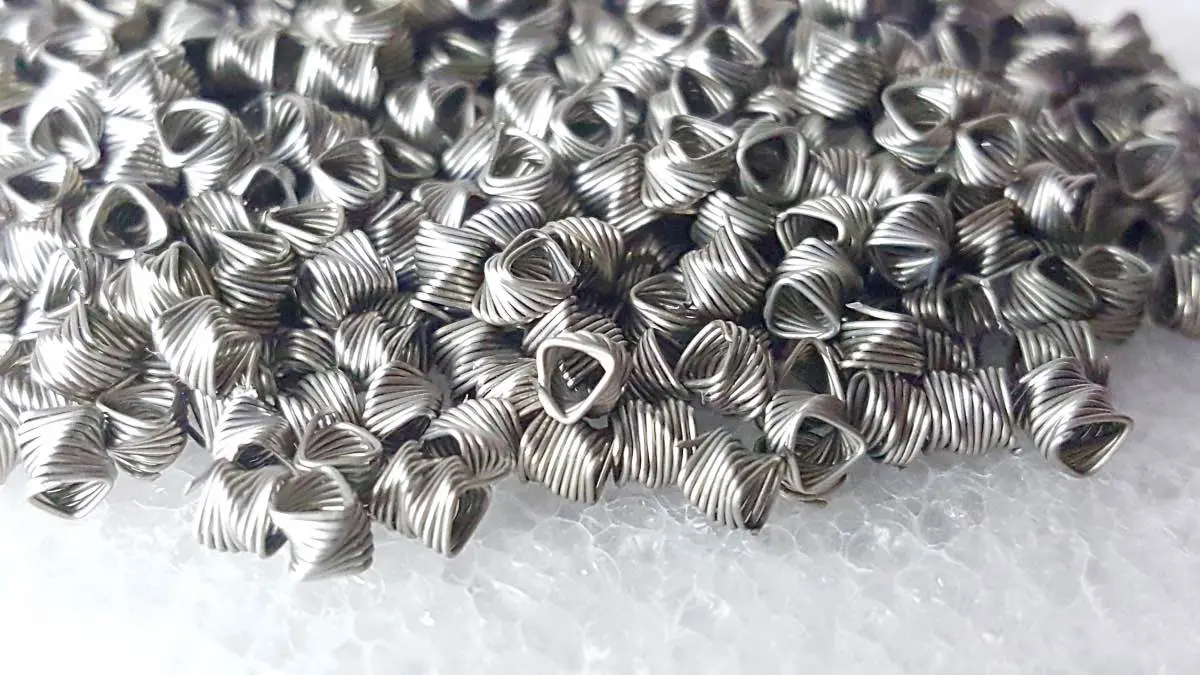
SPN should be poured into the column through the funnel slowly, without shaking or tapping. The main task is the uniformity of laying, without local seals and loosening. It is they that become catalysts for reflux hanging in the column, the beginning of flooding, and reduce the quality of separation and column productivity. Due to poor styling, up to 20% of productivity can be lost. You also need to check the reference point for the nozzle. It is good to use the usual confusion.
If the design provides for various conical nets and other delights, it is worth considering whether they will become catalysts for the lower choke, this is a fairly common occurrence. It is better to throw away these nets, saving yourself a headache. For one on-load tap-changer wad with a string diameter of 1,5 inches, 35 cm of web is needed, for a 2-inch one – 85 cm. Before driving wads, it is recommended to think about their future extraction from the column.
Thermal sensors
Before the column is insulated, it is necessary to place thermal sensors on it. Since the absolute temperature value is not required, but it is necessary to capture changes with an accuracy of 0,1 degrees, it is suitable to place the sensors simply on the surface of the column: in a pocket or glued with aluminum tape under the thermal insulation. There will be no significant difference in the accuracy of readings and inertia (the maximum delay is 5-6 seconds, which is not critical).
Thermometers are required 20 cm from the bottom of the column and 2/3 of its height. Focusing on the readings of temperature sensors, they control the entire process. A thermometer at the top of the column is desirable – 10 cm lower from the top edge of the nozzle, it will help to complete the selection of tailings in time.
It is very useful to install a thermometer-alarm, which will give a sound signal in a timely manner when the temperature at the control point exceeds the set one, so that you can adjust the selection in time. A good option is TS-DS-at with a pipe mount or analogues. In the absence of control automation, this is a very useful device.
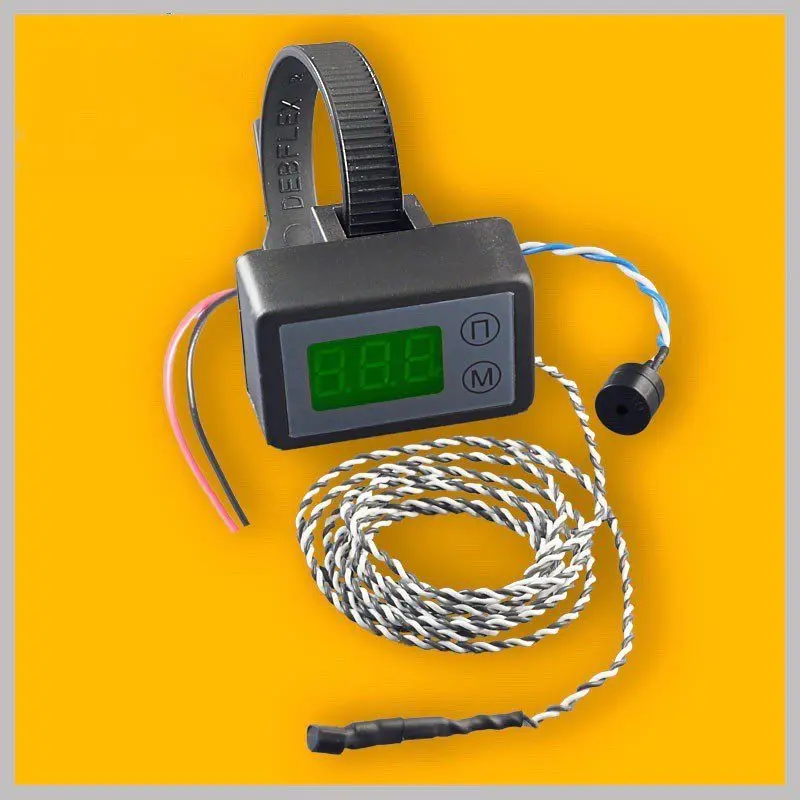
Dephlegmator or condenser
For BC, it is always necessary to connect water to the dephlegmator in parallel, and not in series with the refrigerator, necessarily through different valves. The dephlegmator requires a needle regulating valve. The water drain must be made separate – for visual control of the result of the adjustments.
When using a dimroth, water is supplied to its outer coils, and the valve is placed at the inlet. If a shell-and-tube or shirt is used, then the water is supplied from above, and the tap is placed at the bottom at the outlet. This prevents the dephlegmator from drying out at low water flows, making the process well controlled.
For the RC, the connection principles are the same, but if there is a liquid extraction, then the aftercooler can be connected in series before the condenser. You need to put a hose on the tube for communication with the atmosphere of a reflux condenser with liquid extraction and place it in a bottle to drain the condensate, but make sure that the tube does not become immersed in condensate during operation, otherwise, when the column breathes, the tube will pull the liquid towards itself and the pressure in the cube will decrease by the height of the water column. In this case, the temperature in the cube will be higher than the boiling point, which will lead to rapid boiling and an increased portion of steam entering the dephlegmator, as a result, the pre-choke regime will be replaced by choking.
Insulation of the reflux condenser during liquid extraction will lead to an increase in water consumption, but there will be no benefit. If the selection goes by steam and the water flow is stabilized, then the point in warming the dephlegmator appears. Drafts, sudden changes in ambient temperature – all this can be compensated by making the process more regulated and stable. But if the flow of water through the dephlegmator is not stable and changes even when the tank in the toilet is filled or water is opened in the kitchen, then against the background of this instability, the effect of thermal insulation will be almost imperceptible.
Refrigerator or aftercooler
There are fewer problems here, the water connection is from below, the exit is from above. The tube for draining the product into the jar must necessarily have a jet break, which means that the tube cannot be immersed in condensate.
If a shell-and-tube refrigerator (CCT) is used, then often a drain cup is put on it, which combines all flows from 7-12 CCT tubes and sends it to the selection through one. The glass must have a tube for communication with the atmosphere, this will ensure the break of the jet. Otherwise, a classic swing may begin with the release of spray and foam into the nozzle, flooding of the column, etc.
Other heating sources (gas, induction, electric stove)
On an open fire with alcohol, those who have iron nerves and a warehouse of fire extinguishers work. A gas stove for distillation and beer columns is not uniquely suitable.
Packed column induction cooker is not used due to discrete power control with large steps.
Heating on an electric stove is possible, but it must work with constant heating, and not using start-stop technology (pulse mode). Also, the electric stove must be powered through a voltage stabilizer.
Any stoppage of heating, a drop in input power or a drop in pressure in the water supply leads to a breakdown in the process and a portion of unnecessary impurities enter the selection. But the main rake for all of the above heating methods is in a different place – as the partially insulated cube warms up and its temperature rises, not only heat losses increase, since the temperature difference between the cube and the surrounding air increases, but the heat transfer from the stove to the cube also decreases – useful power heating. This leads to an additional reduction in the volume of generated steam and gradually reduces its speed in the column with all the ensuing consequences. A side effect in the presence of some other design flaws may be partial flooding of the column and choking.
It is possible to obtain alcohol using these heating methods, but its quality will leave much to be desired. If you want a good result, you cannot leave room for chance, you need to ensure the stability and controllability of all processes.
The author of the article is IgorGor.