Contents
The drawer is not just a pipe between a cube and a refrigerator (reflux condenser). From the correct choice of geometric dimensions, material and thermal insulation of the side depends on the productivity, degree of purification, technological modes of distillation and comfortable work with the apparatus as a whole.
Tsarga for moonshine still
In a simple classical distillation, drawers are successfully displacing dry steamers. Solving the problem of combating splashing, the tsargs allow you to simultaneously deal with sulfurous gases, strengthen moonshine, and even to some extent purify the drink from non-volatile compounds due to partial condensation. Another advantage of the drawer is that the equipment becomes less bulky.
The diameter of the drawer is chosen based on the desired performance and the maximum speed of the steam, at which the resulting wild phlegm and splashes that have flown out of the cube along with the steam flow back unhindered, and not be driven up the walls to the refrigerator.
At a steam speed in the side up to 2 m/s, spray entrainment is excluded, from 2 to 3 m/s the result is somewhat worse, and at 3 m/s and above, the steam begins to drive phlegm up the pipe.
Calculating the speed of steam is easy:
V = N * 750 / S (m/s),
where:
- N – power (kW);
- 750 – steam generation (cm3 / s kW)
- S – cross-sectional area of the column on the inner diameter (mm2).
To protect against splashing, in most cases, the height of the drawer is sufficient in the range of 30-40 cm, therefore, only geometric considerations are decisive when choosing a height. Usually proceed from the free vertical placement of the refrigerator to ensure the best conditions for its operation.
The correct length of the moonshine still (classic distiller) is approximately equal to the length of the refrigerator.
Material
Standard drawers are made of copper or stainless steel. Copper acts as a catalyst and helps to bind sulfurous gases, clearing the moonshine of unwanted odors. The use of copper is advisable in the distillation of cereals and some fruit and berry brews in order to obtain noble distillates by repeated fractional distillation.
The copper side does not provide advantages in the distillation of sugar or any other raw material for further distillation or obtaining NDRP in apparatus with liquid extraction, since non-condensable gases and steam in the condenser find different paths. The gas flies out through the TCA (atmospheric communication tube) and does not come into contact with the condensate going to the extraction, and therefore does not dissolve in it. Purification of sulfur dioxide on such devices is simple and does not require additional efforts.
Sometimes, to increase the effect during the first distillation, a copper nozzle (filler) is used. This is a rather controversial technique: the contact area with copper will grow, the purification from sulfurous gases will improve, but at the same time the productivity of the apparatus will decrease, which means that the distillation time will increase, as a result of prolonged boiling of the mash, more other harmful impurities will be released. The measure is important here: if you choose copper rings or tubes as a nozzle, this is one thing, and if you choose a dense nozzle like SPN, it’s completely different.
Dense nozzles have a place in the second stage, at the first stage it is better to limit yourself to just a copper side.
Drawer for distillation and beer columns
When choosing the dimensions of the drawer side for heat and mass transfer processes on beer or distillation columns, the conditions are somewhat more, but they are understandable and natural.
Inner diameter
The cost of the column as a whole significantly depends on the diameter. Increasing the diameter not only increases the cost of the pipes from which the column is made, but also increases the amount of packing required. And the nozzle is one of the most expensive components of the device. For example, for a column one and a half meters high with an inner diameter of 38 mm, 1,7 liters of nozzle are needed, for 48 mm – already 2,7 liters.
The performance of the column is directly proportional to the square of the internal diameter of the side. With an increase in diameter from 38 to 48 mm, productivity will increase by one and a half times. Therefore, choosing, for example, between pipe 52 with a wall of 1 mm or 1,5 mm, you need to understand that the nominal withdrawal rate for the first will be 1800, and for the second – 1700 ml / h. Here is such a price for a seemingly insignificant change in size.
The nominal heating power in Watts and the nominal rate of selection of the “body” milliliters per hour are numerically equal to the cross-sectional area of the drawer, based on the inner diameter. This rule is true when used as a SPN packing, the size of which corresponds to the diameter of the column. For other less or denser nozzles, the numerical values will be different, but the general trend will continue.
The denser the packing, the lower the performance of the column. True, this is compensated by a better separating ability. If we talk about SPN and rectification, then the optimal size of the nozzle should be 12-14 times smaller than the inner diameter of the side. When getting fortified moonshine or NRLP, the cleaning requirements are much lower, so you can use a larger nozzle, shifting the focus towards performance.
Height
It is the height of the mounted part of the tsarg that largely determines the separating ability of the column. This indicator should not be confused with the height of the tsargi. Manufacturers often mislead buyers with their unsuccessful designs. For example, the height of the drawer is 40 cm, but of them the lower empty space is 5 cm, another 3 cm is taken by the structure to support the nozzle, and on top – a device for fixing the nozzle 2 cm high and an empty place for foam to the dephlegmator – 5 cm. As a result nozzles in 40 cm of the tsarge is not 40 cm, but only 25 cm! Even if you put three of them in a row, you won’t get rectified alcohol.
The same applies to the use of one tsargi 1,5 meters long or three 50 cm each. At first glance, there is no difference, but if you take a closer look and calculate the height of the nozzle, then everything is not so simple.
For a clear division into fractions and separation of the “heads”, the nozzle part must be at least 1 meter high, and the height of one side must be no more than 1,5 meters.
With a shorter length, the separating ability will be insufficient for a clear selection of “heads”. The limitation of 1,5 meters is due to the fact that the efficiency of the packed column changes unevenly with increasing height. For example, increasing the length from 50 to 60 cm will give the same increase in separation power as from 120 to 150 cm (figures are arbitrary and are given to show the trend). The height of the nozzle part in one side should be no more than 30 of its internal diameters.
The benefit of a further increase in height is negated by the channel and wall effects. If you want to build a higher column, you need to divide it into several tsargs or use phlegm concentrators – devices that divert phlegm from the walls and direct it to the center of the nozzle. But the use of concentrators often leads to early choking of the column, especially with inept execution. And if there are grids in the design, then in most cases choking becomes a regularity.
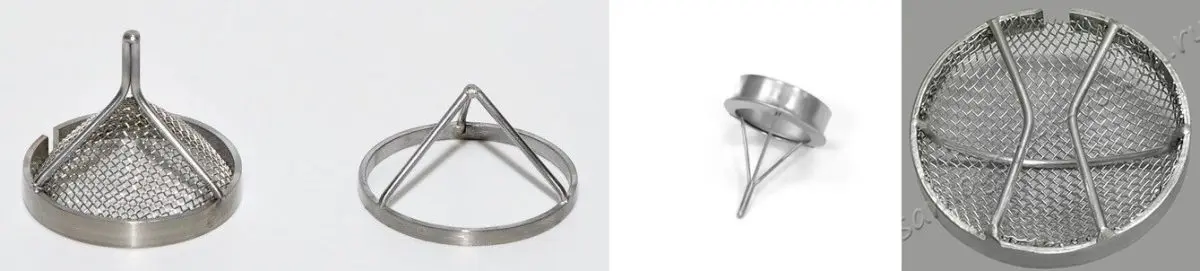
Influence of the height of the drawer side on technological indicators
Suppose that there are well-insulated and vertically exposed two-inch columns 1,2 and 1,8 meters long. Increasing the height of the column by 1,5 times will increase the volume of distilled bottom bulk by the same one and a half times, since the holding capacity and volume of the packing will increase. It will be possible to proceed to the selection of “tails” later, significantly reducing their volume. But you have to pay for everything – the selection time will increase, as well as the volume of “heads” and “head restraints”.
In order to “feel” the order of numbers, we present a table with the volumes and time of selection of various fractions during the distillation of 40 liters of moonshine:
Column height (m) | 1.2 | 1.8 |
Head selection (hour) | 6 | 8 |
Heads (ml) | 120 | 350 |
Headrests (L) | 700 | 1000 |
Tails (l) | 1,5-2 | 0,5-1 |
The rate of “body” selection will be almost the same, and the transition temperature from “body” to “tails” selection will change from 94-95 degrees to 97. However, this will depend on the sense of smell of the column operator. In both cases, a product of approximately the same quality will be obtained.
The wall thickness of the column should be in the range of 1-1,5 mm. This thickness is thermally transparent and allows one to measure temperatures with a negligibly small delay. If temperature sensors are attached with aluminum tape to the surface of the columns under thermal insulation, this will be enough for normal process control.
Increasing the wall thickness will only increase the cost and weight of the column. This makes the structure less stable and imposes additional requirements on the strength of the cube lid.
The correct choice of the dimensions of the drawer is not difficult, it is only necessary to take into account their influence on the technological parameters of the process and compliance with the tasks set.
Even if the funds allow, it is important to avoid the most important mistake – megalomania.
With an increase in diameter, not only productivity changes. Small diameter columns (25-30 mm) require special attention. It is problematic to use a nozzle in them, to center the phlegm flowing down from the reflux condenser, and in general to achieve at least a confident cut-off of the “tails”, not to mention the retention of intermediate impurities.
Columns of medium diameter (35-55 mm) are calm and balanced, work clearly and predictably.
Large diameter columns (more than 57 mm) are more difficult to set up for stable operation, they are productive, but are prone to various sores that nullify the benefit of increased speed. Large columns suffer from spontaneous channel formation: when standard power is supplied, the pressure in the cube does not increase, and the column does not choke. When changing the nozzle to a smaller one, everything stabilizes, but the performance becomes the same as for columns that are much smaller in diameter. Therefore, columns, starting from a diameter of 57 mm, are equipment for experienced distillers who want creativity.
The author of the article is IgorGor.