Contents
In rooms heated using underfloor heating technology, the feeling is much more comfortable than with a traditional radiator system. When the floor is heated, the temperature is distributed in an optimal way: it is warmest for the feet, and at head level it is already cooler. There are two ways of heating: water and electric. The water one is more expensive to install, but cheaper to operate, so that’s what they do more often. You can slightly reduce installation costs if you make a water-heated floor with your own hands. The technology is not the easiest, but it does not require encyclopedic knowledge.
The device and the principle of operation
For water heating of a warm floor, a system of pipes is used through which the coolant circulates. Most often, pipes are poured into a screed, but there are dry installation systems – wooden or polystyrene. In any case, there is a large number of small cross-section pipes laid under the floor covering.
Where can you mount
Due to the large number of pipes, water heating is done mainly in private homes. The fact is that the heating system of high-rise buildings of early construction is not designed for this method of heating. It is possible to make a warm floor from heating, but there is a high probability that either you will be too cold, or your neighbors from above or below – depending on the type of power supply to the system. Sometimes the entire riser becomes cold: the hydraulic resistance of the water floor is several times higher than that of the radiator heating system and it can clog the movement of the coolant. For this reason, it is very difficult to obtain permission from the management company to install a warm floor (installation without permission is an administrative offense).
The good news is that two systems have begun to be made in new buildings: one for radiator heating, the second for underfloor heating. In such houses, permission is not required: an appropriate system was developed taking into account the higher hydraulic resistance.
Organization principles
To understand what you need in order to make a water heated floor with your own hands, you need to understand what the system consists of and how it works.
Heat carrier temperature control
In order to feel comfortable on the floor, the temperature of the coolant should not exceed 40-45°C. Then the floor warms up to comfortable values - about 28 ° C. Most heating equipment cannot produce such a temperature: at least 60-65 ° C. The exception is condensing gas boilers. They show maximum efficiency at low temperatures. From their outlet, the heated coolant can be supplied directly to the pipes of the warm floor.
When using a boiler of any other type, a mixing unit is required. In it, the cooled coolant from the return pipeline is added to the hot water from the boiler. You can see the composition of this bond on the diagram for connecting a warm floor to a boiler.
The principle of operation is the following. The heated coolant comes from the boiler. It enters the thermostatic valve, which, when the temperature threshold is exceeded, opens the water admixture from the return pipeline. In the photo there is a jumper in front of the circulation pump. A two-way or three-way valve is installed in it. Open it and mix in the cooled coolant.
The mixed flow through the circulation pump enters the thermostat, which controls the operation of the thermostatic valve. When the set temperature is reached, the flow from the return is stopped, when it is exceeded, it opens again. This is how the temperature of the coolant of the water heated floor is adjusted.
Contour distribution
Next, the coolant enters the distribution comb. If a water-heated floor is made in one small room (a bathroom, for example), in which only one pipe loop is laid, this node may not exist. If there are several loops, then it is necessary to somehow distribute the coolant between them, and then somehow collect it and send it to the return pipeline. This task is performed by a distribution comb or, as they are also called, a floor heating collector. In fact, these are two pipes – on the supply and return lines, to which the inputs and outputs of all underfloor heating circuits are connected. This is the easiest option.
If a warm floor is made in several rooms, then it is better to install a collector with the ability to adjust the temperature. Firstly, different rooms require different temperatures: someone prefers +18°C in the bedroom, someone needs +25°C. Secondly, most often, the contours have different lengths, and different amounts of heat can be transferred. Thirdly, there are “internal” rooms – which have one wall facing the street, and there are corner ones – with two or even three outer walls. Naturally, the amount of heat in them should be different. This is provided by combs with thermostats. The equipment is not cheap, the circuit is more complicated, but such an installation allows you to maintain the desired temperature in the room.
There are different thermostats. Some control the temperature of the air in the room, the second – the temperature of the floor. You choose the type. Regardless of this, they control the servomotors mounted on the feed comb. Servo motors, depending on the command, increase or decrease the flow area, adjusting the intensity of the coolant flow.
Theoretically (and practically it happens), situations may arise when the supply to all circuits is blocked. In this case, the circulation will stop, the boiler may boil and fail. To prevent this from happening, be sure to make a bypass through which part of the coolant passes. With this construction of the system, the boiler is safe.
You can see one of the system options in the video.
Laying a warm water floor
One of the key components of the system is pipes and their fixation system. There are two technologies:
- Dry – polystyrene and wood. Metal strips with formed channels for laying pipes are laid on a system of polystyrene foam mats or wooden plates. They are necessary for a more even distribution of heat. Pipes are inserted into recesses. Rigid material is laid on top – plywood, OSB, GVL, etc. A soft floor covering can be laid on this base. It is possible to lay tiles on tile adhesive, parquet or laminate.
Wooden water floor heating system - Laying in a coupler or so-called “wet” technology. It consists of several layers: insulation, fixation system (tapes or mesh), pipes, screed. On top of this “pie”, after setting the screed, the floor covering is already laid. If necessary, a layer of waterproofing is laid under the insulation so as not to flood the neighbors. A reinforcing mesh may also be present, which is laid over the floor heating pipes. It redistributes the load, preventing damage to the system. A mandatory element of the system is a damper tape, which is rolled around the perimeter of the room and placed at the junction of two circuits.
Water heated floor in screed
Both systems are not ideal, but laying pipes in a screed is cheaper. Although it has a lot of disadvantages, it is because of its lower cost that it is more popular.
Which system to choose
In terms of cost, dry systems are more expensive: their components (if you take ready-made, factory ones) cost more. But they weigh much less and are put into operation faster. There are several reasons why you should use them.
First: the heavy weight of the screed. Not all foundations and ceilings of houses are able to withstand the load created by a water-heated floor in a concrete screed. Above the surface of the pipes there must be a concrete layer of at least 3 cm. If we take into account that the outer diameter of the pipe is also about 3 cm, then the total thickness of the screed is 6 cm. The weight is more than significant. And on top there is often a tile on a layer of glue. Well, if the foundation is designed with a margin, it will withstand, and if not, problems will begin. If there is a suspicion that the ceiling or foundation will not withstand the load, it is better to make a wooden or polystyrene system.
Second: low maintainability of the system in the screed. Although it is recommended to lay only solid coils of pipes without joints when laying underfloor heating contours, periodically the pipes are damaged. Either during the repair they hit with a drill, or burst due to marriage. The place of damage can be determined by a wet spot, but it is difficult to repair: you have to break the screed. In this case, adjacent loops can be damaged, due to which the damage zone becomes larger. Even if you managed to do it carefully, you have to make two seams, and they are the potential sites for the next damage.
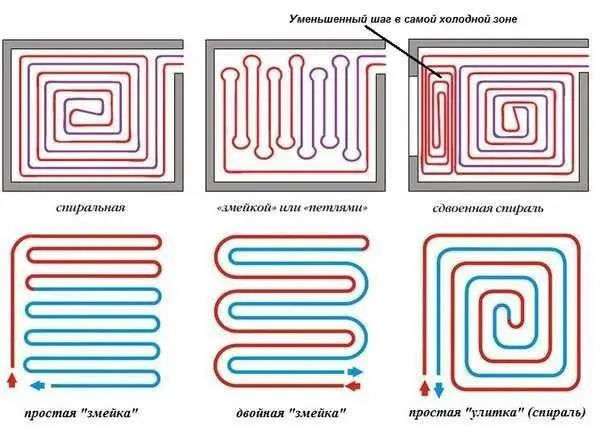
Third: the commissioning of a warm floor in a screed is possible only after the concrete has gained 100% strength. This takes at least 28 days. Before this period, it is impossible to turn on the warm floor.
Fourth: you have a wooden floor. By itself, a tie on a wooden floor is not the best idea, but also a screed with an elevated temperature. The wood will quickly collapse, the whole system will collapse.
The reasons are serious. Therefore, in some cases, it is more expedient to use dry technologies. Moreover, a do-it-yourself wooden water-heated floor is not so expensive. The most expensive component is metal plates, but they can also be made from thin sheet metal and, better, aluminum. It is important to be able to bend, forming grooves for pipes.
A variant of a polystyrene underfloor heating system without a screed is shown in the video.
Materials for a warm water floor
Most often they make a water-heated floor in a screed. Its structure and necessary materials will be discussed. The scheme of a warm water floor is presented in the photo below.

All work begins with leveling the base: without insulation, heating costs will be too high, and insulation can only be laid on a flat surface. Therefore, the first step is to prepare the base – make a rough screed. Next, we describe step by step the procedure for work and the materials used in the process:
- A damper tape is also rolled around the perimeter of the room. This is a strip of heat-insulating material, no more than 1 cm thick. It prevents heat loss for wall heating. Its second task is to compensate for the thermal expansion that occurs when materials are heated. The tape can be special, and you can also lay thin foam cut into strips (no more than 1 cm thick) or other insulation of the same thickness.
- A layer of heat-insulating materials is laid on the rough screed. For underfloor heating, the best choice is polystyrene foam. The best is extruded. Its density must be at least 35kg / m2. It is dense enough to support the weight of the screed and operating loads, has excellent performance and a long service life. Its disadvantage is that it is expensive. Other, cheaper materials (polystyrene, mineral wool, expanded clay) have a lot of disadvantages. If possible, use polystyrene foam. The thickness of the thermal insulation depends on many parameters – on the region, the characteristics of the foundation material and insulation, the method of organizing the subfloor. Therefore, it must be calculated for each case.
- Further, a reinforcing mesh is often laid in increments of 5 cm. Pipes are also tied to it – with wire or plastic clamps. If expanded polystyrene was used, you can do without reinforcement – you can fasten it with special plastic brackets that are driven into the material. For other heaters, a reinforcing mesh is required.
- Beacons are installed on top, after which the screed is poured. Its thickness is less than 3 cm above the level of the pipes.
- Next, a clean floor covering is laid. Any suitable for use in an underfloor heating system.
These are all the main layers that need to be laid when you make a do-it-yourself water-heated floor.
Underfloor heating pipes and laying schemes
The main element of the system is pipes. Most often, polymeric ones are used – made of cross-linked polyethylene or metal-plastic. They bend well and have a long service life. Their only obvious drawback is not too high thermal conductivity. This minus is not present in the recently appeared corrugated stainless steel pipes. They bend better, cost no more, but due to their low popularity, they are not often used yet.
The diameter of pipes for underfloor heating depends on the material, but usually it is 16-20 mm. They fit in several schemes. The most common are spiral and snake, there are several modifications that take into account some features of the premises.
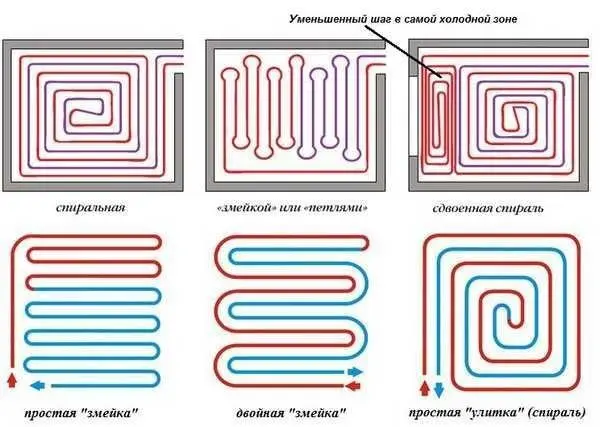
Laying with a snake is the simplest, but passing through the pipes the coolant gradually cools down and by the end of the circuit it is already much colder than it was at the beginning. Therefore, the zone where the coolant enters will be the warmest. This feature is used – laying starts from the coldest zone – along the outer walls or under the window.
This drawback is almost devoid of a double snake and a spiral, but they are more difficult to lay – you need to draw a diagram on paper so as not to get confused when laying.
Screed
You can use a conventional cement-sand mortar based on Portland cement to fill a water-heated floor. The brand of Portland cement should be high – M-400, and preferably M-500. Concrete grade – not lower than M-350.
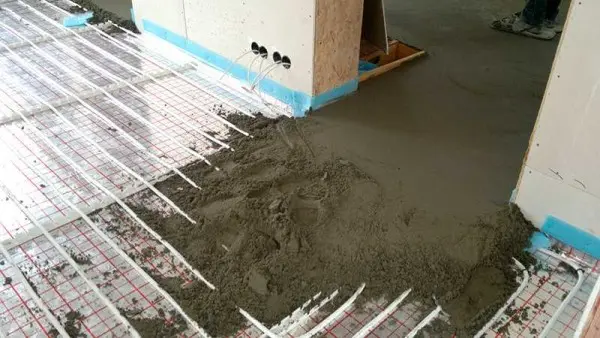
But ordinary “wet” screeds gain their design strength for a very long time: at least 28 days. All this time it is impossible to turn on the warm floor: cracks will appear that can even break the pipes. Therefore, so-called semi-dry screeds are increasingly being used – with additives that increase the plasticity of the solution, significantly reducing the amount of water and the time for “aging”. You can add them yourself or look for dry mixes with the appropriate properties. They cost more, but there is less trouble with them: according to the instructions, add the required amount of water and mix.
It is realistic to make a water heated floor with your own hands, but it will take a decent amount of time and a lot of money.