Contents
Tray distillation columns have little reinforcing power and are traditionally used in the production of whiskey, cognac and other noble liquors. A small number of plates allows you to save the organoleptic of raw materials with high stability and productivity of the apparatus.
Material
Copper dish-shaped columns with viewing windows are called flutes because of their similarity, and those made in a glass case are called crystal. It is clear that these names are just a marketing ploy and have nothing to do with the design itself.
Copper is an expensive material, so the approach to its processing is thorough. A brass flute from leading manufacturers is a work of art and a source of their pride. The cost of the product can be absolutely any amount that the buyer is willing to spend.
Slightly cheaper than a flute in a stainless steel case, and the most budget option is in a glass case.
Design features and types of dish columns
The most widespread are modular column designs based on branch tees or cylinders made of borosilicate glass. Naturally, this is a large number of extra connecting parts and an overestimated cost.
A simpler option is ready-made blocks for 5-10 plates. Here the choice is wider, and the price is more moderate. As a rule, this option is made in glass cases.
There are also quite budget options – just inserts for existing drawers.
They can be recruited from components in any required quantity.
The design may be different, but if such tray columns are used with metal flasks, the visibility of the process is lost. It is much more difficult to understand what mode the column is operating in, and this is very important for working with trays.
To seal each floor, simple silicone discs are used.
Naturally, this is less reliable than sealing gaskets in modular designs, but in general they work well.
As an alternative, there is a simplified modular design, where each floor is assembled from simple and inexpensive parts, and the entire structure is pulled together with studs.
The advantage of modular columns is primarily their maintainability and openness to modifications. For example, it is easy to supplement the column at the required level with an intermediate fractionation unit and a fitting for a thermometer. All you have to do is change the plate.
Sieve tray columns are a cheaper option. This does not mean that the quality of the product with their use will be worse. But they require more precise control.
Dip trays are even cheaper, but their operating range is very narrow, so you need to be prepared for precise heat control with power stabilized sources. Basically, failed trays are used at the NSC.
The most common materials for making cymbals are copper, stainless steel and fluoroplastic. Any combination is possible. Copper and stainless steel are familiar materials, fluoroplastic is one of the most inert materials, comparable to platinum. But its wettability is poor.
If we compare a fluoroplastic plate with a stainless one, then it will be flooded much faster.
The number of plates in the column is usually limited to 5 for distillates with a strength of 88-92% and 10 for purified distillates with a strength of up to 94-95%.
Modular columns allow you to make a set of the required number of plates from various materials.
Difference Between Packed Column and Tray Column
“I have a packed column, do I need a tray?” – this question sooner or later confronts every distiller. Both columns implement the heat and mass transfer technology, but there are significant differences in their operation.
Number of reinforcement steps
The packed column operates in the maximum separation mode at the pre-choke capacity. By adjusting the reflux ratio, it is possible to change the number of theoretical plates in a wide range: from zero to infinity (with the reflux condenser completely turned off and the column working on itself).
The tray column is characterized by a structurally specified number of separation stages. One physical plate has an efficiency of 40 to 70%. In other words, two physical plates give one stage of separation (strengthening, theoretical plate). Depending on the operating mode, the efficiency does not change so much as to significantly affect the number of steps.
holding capacity
A packed column with its low holding capacity makes it possible to well purify the distillate from the head fraction and somehow contain the tail fraction.
The tray column has an order of magnitude greater holding capacity. This prevents her from doing such a hard cleaning of the “heads”, but allows her to perfectly contain the tails. That is, to align the distillate in terms of chemical composition. At the same time, the more you need to clean the distillate from impurities, the more plates you need to put. A simple problem that can be practically solved. Once you have found the optimal number of plates for yourself and you don’t think about it anymore.
Sensitivity to control actions
The packed column is very sensitive to the difference in water pressure in the reflux condenser or to changes in heating power. A slight change in them leads to a change in the number of strengthening steps at times or even dozens of times.
The efficiency of plates can change by a maximum of 1,5 times, and even then with a very large and targeted change in these parameters. It can be considered that a tuned tray column, in terms of separating power, will practically not respond to the usual small drops in water pressure or voltage.
Performance
The performance of a packed column mainly depends on its diameter. The optimal diameter for modern nozzles is 40-50 mm, with a further increase in the diameter, the stability of the processes decreases. Near-wall effects and channel formation begin to manifest themselves. Disc columns do not suffer from such weaknesses. Their diameter and productivity can be increased to any required value. If only there was enough heating power.
Technological features of obtaining aromatic distillates
When using packed columns to limit the degree of strengthening, we are forced to use shorter sides and a larger packing. Otherwise, the esters that give the main flavor to the distillate will create azeotropes with impurities of the head fraction, then quickly fly out of the cube. We select the “heads” shortly, the “body” – at an increased speed. As for the “tails”, the small number of nozzles and the short tsarga do not completely contain the fuselage. It is necessary to switch to the selection of tail fractions earlier or to work with small cubic bulks.
The tray column has a relatively large holding capacity, so there are no issues with holding the fusel oil. For the selection of “heads” and “body” 5-10 physical plates give 3-5 steps of strengthening. This allows distillation according to the rules of conventional distillation. Calmly, without the risk of depriving the distillate of aroma, select the “heads”, and when collecting the “body” do not think about the premature approach of the “tails”. Fogging on the lower plates at the end of the selection will clearly let you know about the need to change the container. The degree of cleaning can be set by changing the number of plates.
Five or ten plates are not enough to get close to alcohol in terms of purification, but it’s realistic to get into the GOST requirements for distillate.
The use of tray columns in the distillation of fruit or grain raw materials, especially for further aging in barrels, greatly simplifies the distiller’s life.
Fundamentals of sizing column trays
Consider the designs of the most common plates for domestic purposes.
Failed plate
At its core, this is just a plate with holes, which can be round, rectangular, etc.
The phlegm flows into relatively large holes towards the steam, which determines the main disadvantage of failed plates – the need for precise control of the set mode.
A slight decrease in the heating power leads to the fact that the entire phlegm falls into the cube, and an increase in power locks the phlegm on the plate and leads to choking. These trays can operate satisfactorily over a relatively narrow load range, where they are quite competitive.
The simplicity of design and high performance of dip trays, along with the usual heating in home distilling by heating elements with a voltage stabilized power source, has led to their widespread use for continuous beer columns (NBK), which, in combination with a borosilicate or quartz glass body, makes column tuning simple and visual.
To calculate the number and diameter of holes, the bubbling conditions are taken into account. It has been experimentally determined that the total area of the holes should be equal to 15-30% of the plate area (pipe section). In the general case, for BK of periodic action, the base diameter of the holes is about 9-10% of the diameter of the column allows you to get into the working area.
The diameter of the holes of the failure trays for the NSC is selected based on the properties of the raw material. If, when distilling sugar mash and wine, holes with a diameter of 5-6 mm are sufficient, then when distilling flour jams, a hole diameter of 7-8 mm is preferable. However, trays for NSC have their own calculation features, since the vapor density varies significantly along the height of the column, the dimensions must be calculated for each tray separately, otherwise their performance will be far from optimal.
Sieve plate with overflow
If the diameters of the holes of the failed plate are less than 3 mm, then even at a relatively low power, the phlegm will be locked on the plate and without additional overflow devices, it will be flooded. But a sieve tray equipped with such devices significantly expands its operating range.
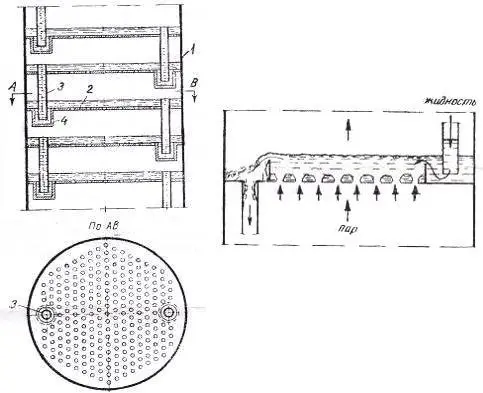
1 – body; 2 – sieve plate; 3 – overflow tube; 4- glass
With the help of overflow devices on these plates, the maximum level of reflux is set, which allows you to avoid early flooding and more confidently work with a high steam load. This does not prevent the phlegm from completely merging into a cube when the heating is turned off, and the column will have to be restarted from scratch, as is usual for all failed plates.
In a simplified calculation of such plates, the following relationships are taken into account:
- the total area of the holes is 7-15% of the pipe cross-sectional area;
- the ratio between the diameters of the holes and the pitch between them is about 3,5;
- the diameter of the drain pipes is approximately 20% of the diameter of the dish.
Water seals must be installed in the drain holes to avoid steam breakthrough. Sieve plates must be installed strictly horizontally to allow steam to pass through all the holes and to prevent reflux from flowing through them.
capped plates
If, instead of holes in the plates, we make steam pipes higher than the drain pipes, and cover them with slotted caps, we get a completely new quality. These plates will not drain the phlegm when the heat is turned off. The phlegm divided into fractions will remain on the plates. Therefore, to continue working, it will be enough to turn on the heating.
In addition, such plates have a structurally fixed reflux layer on the surface, they operate in a wider range of heating powers (steam loads) and changes in reflux ratio (from complete absence to complete return of reflux).
It is also important that capped plates have a relatively high efficiency – about 0,6-0,7. All this, along with the aesthetics of the process, determines the popularity of cap cymbals.
When calculating the construct, the following proportions are taken into account:
- the area of the steam tubes is about 10% of the section of the column;
- the area of the slots is 70-80% of the area of the steam pipes;
- drain area 1/3 of the total area of the steam pipes (diameter approximately 18-20% of the diameter of the pipe section);
- the lower plates are designed with a high level of reflux and a large section of the slots so that they work as holding ones;
- top plates are made with less reflux and slots so that they work as separating ones.
Based on the graphs given by Stabnikov, we see that with a reflux layer of 12 mm (curve 2), the maximum efficiency is achieved at a steam velocity of the order of 0,3-0,4 m/s.
For a 2” column with an internal diameter of 48 mm, the required net heating power is:
N = V * S / 750;
where:
- V is the steam velocity in m/s;
- N is the power in kW, S is the sectional area of the column in mm².
N = 0,3 * 1808/750 = 0,72 kW.
You might think that 0,72 kW determines a small performance. Perhaps, taking into account the available power, it is worth increasing the diameter of the column? It’s probably right. Common diameters of quartz glasses for diopters are 80, 108 mm. Let’s take 80 mm with a wall thickness of 4 mm, an inner diameter of 72 mm, a cross-sectional area of 4069 mm². Let’s recalculate the power – we get 1,62 kW. Well, it’s better, it’s suitable for a home gas stove.
Having chosen the diameter of the column and the design capacity, we determine the height of the overflow pipe and the distance between the plates. To do this, we use the following equation:
V = (0,305 * H / (60 + 0,05 * H)) — 0,012 * Z (м/с);
where:
- H is the distance between the plates;
- Z is the height of the overflow tube (i.e. the thickness of the reflux layer on the plate).
The steam speed is 0,3 m/s, the height of the plate should not be less than its diameter. For lower plates, the height of the reflux layer is larger. Smaller for the top.
Let’s calculate the closest combinations of plate and overflow heights, mm: 90-11; 100-14; 110-18; 120-21. Considering that standard glass has a height of 100 mm, for a modular design we choose a pair of 100-14 mm. Naturally, this is just our choice. You can take more, then the protection against spray will be better with an increase in power.
If the design is not modular, then there is more room for creativity. You can make the lower plates with a larger holding capacity of 100-14, and the upper one with a larger separation – 90-11.
We choose caps from standard and available sizes. For example, plugs for a copper pipe 28 mm, steam pipes – a pipe 22 mm. The height of the steam pipe must be greater than that of the overflow pipe, say 17 mm. The gaps for the passage of steam between the cap and the steam pipe must have a larger cross-sectional area than that of the steam pipe.
Slots for the passage of steam in each cap are required with a cross-sectional area of u0,75buXNUMXbabout XNUMX of the area of uXNUMXbuXNUMXbthe steam pipe. The shape of the slots does not play a special role, but it is better to make them as narrow as possible so that the steam breaks into smaller bubbles. This increases the area of contact between the phases. Increasing the number of caps also benefits the process.
Tray column operating modes
Any bubble columns can operate in several modes. At low steam velocities (low heating power), a bubble regime occurs. Steam in the form of bubbles moves through the phlegm layer. The phase contact surface is minimal. With an increase in the steam velocity (heating power), individual bubbles at the exit from the slots merge into a continuous jet, and after short distances, due to the resistance of the bubbling layer, the jet breaks up into many small bubbles. An abundant foam layer is formed. The contact zone is maximum. This is foam mode.
If we continue to increase the steam supply rate, then the length of the steam jets increases, and they reach the surface of the bubbling layer without collapsing, forming a large amount of splashes. The contact area decreases, the efficiency of the plate decreases. This is a jet or injection mode.
The transition from one regime to another has no clear boundaries. Therefore, even when calculating industrial columns, only steam velocities are determined according to the lower and upper limits of work. The operating speed (heating power) is simply chosen in this range. For home columns, a simplified calculation is carried out for a certain average heating power, so that there is an opportunity for adjustments during operation.
Those wishing to make more accurate calculations can recommend the book by A.G. Kasatkin “Basic processes and apparatuses of the chemical industry”.
P.S. The foregoing is not a complete methodology that allows you to calculate the optimal dimensions of each plate in relation to any specific case and does not claim to be accurate or scientific. But still, this is enough to make a working dish column with your own hands or to understand the advantages and disadvantages of the columns offered on the market.
The author of the article is IgorGor.